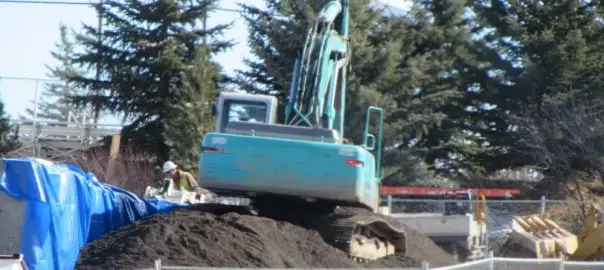
360 Excavator & Hazard Spotting
There are many hazards and risk factors associated with operating a 360 excavator on a jobsite. According to Occupational Safety and Health Administration (OSHA), around 20 to 25 employees die each year due to excavation-related accidents. They also state that excavation and trenching operations pose a higher fatality rate than the risk for general construction work.
Employers have a responsibility to provide a hazard-free work environment for their employees, and if they cannot do that, they must provide the proper programs and resources to eliminate or avoid the hazards.
Employees have a responsibility to follow all safety policies and rules implemented in their workplace. They are required to actively participate in their safety training and apply what they have learned throughout everyday tasks in the workplace.
Overall, everybody has a part to play in workplace safety, and identifying hazards plays a big part in the safety of everyone in the workplace. Before jumping into how to accomplish this, we will first dive into what hazard spotting and 360 excavators are.
What Is Hazard Spotting?
Hazard spotting is simply another way to say identifying hazards, which is the first step in the risk management process. The goal of hazard spotting is to assist you in identifying hazards in order to reduce potential accidents in your workplace. Hazards that go unnoticed will have nothing in place to keep them from escalating into a dangerous situation, resulting in a possible injury or death.
What Is a 360 Excavator?
An excavator is a large, typically tracked machine that digs trenches and holes deep into the ground using a bucket attached to a long boom and pick assembly. A 360-degree excavator is one that can pivot completely around its tracked base. This enables the driver to pick up substantial quantities of dirt or other materials and move them anywhere inside the vehicle’s sphere of influence.
To ensure the safety of everyone on the worksite, all employees must follow standards and adhere to the established safety measures.
Spotting Hazards as a 360 Excavator Operator
As previously mentioned, if proper precautions and training are not implemented correctly in the workplace, excavation work can be a dangerous activity and present a high risk of injury or fatality to employees. Due to this, it is crucial to know how to spot hazards that are present in your work environment. The steps you should take in spotting hazards in the workplace are:
- Know your worksite and operations
- Perform a risk assessment
- Spot the hazard and identify the risks
- Implement safety controls
Know Your Worksite & Operations
Operators need to be familiar with the worksite where they will be operating the excavator. This will ultimately help you to operate safely and prevent any accidents. There are many factors to consider when it comes to being able to understand your worksite and the operations you will be performing.
Ground Conditions
Inspect the site for potholes, areas of soft soil, or any other obstructions that could impede mobility or cause tipping. Weather can change ground conditions drastically. Ice, mud, or bumpy ground can decrease traction or affect the machine’s center of gravity.
Clarify which soil you will move and what procedures you will use to remove it. Consider how deep you’ll be excavating and how this will affect ground conditions. If the excavation needs to be backfilled, consider what material you will use.
Power Lines
Find out if you will be working with or around power lines. Power lines can electrify the boom and body of the machine even before the arm touches the lines. To prevent this, regulations state that all machinery must stay at least 10 feet (3 m) away from power lines, though the exact distance can vary by locality.
If coming into close proximity with power lines is unavoidable, utility companies need to be contacted to de-energize the lines while work is being done in that area. However, these situations are rare, and you should always avoid coming close to lines.
Lighting
When planning the job, you’ll need to consider whether you’ll be working at night or in dark conditions. If so, plan for a way to provide appropriate lighting because using the lights on the excavator or the headlights of other vehicles will be insufficient. Providing the proper lighting will dramatically improve visibility, which increases the safety of your worksite.
Pedestrians
Pedestrians always have the right of way. That being said, pedestrians might not always put themselves in the safest position or be aware of your presence. On busy worksites or areas of travel, it’s common for workers or pedestrians to be focused only on what they’re doing.
You, as a heavy equipment operator, must always be aware of your surroundings and work responsibly to keep people safe. Take the time to orient yourself on the site, and be aware of pedestrians and other workers.
Traffic
If your job takes place near roads or parking lots, use barriers, cones, caution tape, and flaggers to safely keep traffic away from your work area. Place these flaggers and cones so drivers will have enough time to slow down and avoid dangerous work areas.
Perform a Risk Assessment
OSHA requires every workplace to perform and record a risk assessment. There are two essential steps in conducting a risk assessment. The following sections will describe both in detail.
Identifying the Risk
Before a risk assessment can take place, you should strive to identify as many hazards on the site as possible. There are many places that you can look to identify the possible hazards on your site. A great way to do this is by collecting and consulting existing information. Some of these resources could include:
- Safety data sheets (SDSs)
- Job hazard analysis reports
- Incident investigation reports
- Exposure monitoring results
The faster you identify a hazard, the sooner that hazard can be controlled, thus minimizing the overall risk of injury, illness, or fatality in the workplace.
Evaluate the Risks
Conducting a proper risk assessment is all about asking the right questions. These questions fall under three primary categories:
- The level of severity
- The level of exposure
- The likelihood of employee injury of an incident occurring on your jobsite.
Once all the listed values are calculated, add the total values for severity, exposure, and likelihood together to find the hazard’s overall risk using a risk matrix. A risk matrix is a tool that helps you visualize the probability that an incident will occur and the severity of the impact if an incident does occur.
Organize Hazards
Once you have calculated the overall risk of all hazards, organize the hazards from highest to least amount of risk. Your top priority should be to control the hazards which pose the highest possible risk of injury, illness, and fatality in the workplace.
Implementing Safety Controls
The hierarchy of controls provides five methods that you can use to control the hazards that you’ve identified and assessed. These five methods are as follows:
Elimination
Elimination is the most effective control measure, and therefore, should be the first method that you try to implement. As the name suggests, this method strives to eliminate the hazard before an incident occurs. Despite the effectiveness and generally lower cost, elimination is not always possible, especially if job procedures are already put in place.
Substitution
Substitution is the second control measure that you should try to employ. It is the process of removing harmful materials and replacing them with safer ones. Substitution, like elimination, is difficult to employ once procedures are put in place; therefore, you should strive to implement this method as processes are being developed if possible. Take special care not to replace one hazard with a different one. Substitution is only effective if the replacement for the hazard doesn’t pose a risk to your employees.
Engineering Controls
After you have ruled out elimination and substitution as possibilities for controlling the hazard, the other three methods can be considered. Engineering controls refer to the process of making a physical change to the workplace in order to remove the hazard.
Administrative Controls
Administrative controls change the way that people work. These controls are established by industry regulations. However, you must ensure that your employees are familiar with these policies and how they apply to the workplace.
Personal Protective Equipment
Personal protective equipment (PPE) is the least effective control method. PPE is designed to prevent injury or illness that could be caused by a specific hazard. Ensure the use of PPE when other controls can’t provide sufficient protection for your employees.
Common Hazards Associated With 360 Excavators
Now that you know the process of spotting and avoiding hazards on the worksite, we are going to discuss the most common excavator hazards. As stated previously, knowing what hazards to expect on the jobsite decreases the likelihood of an incident.
Environmental Hazards
Be aware of any environmental hazards while operating the machine. When working in scrap, make sure to remove any debris or wire that may damage or wrap around rollers or other components of your machine. In cold climates, run the machine on a dry plot of ground both forward and reverse before shutting down to remove moisture and prevent the tracks from freezing.