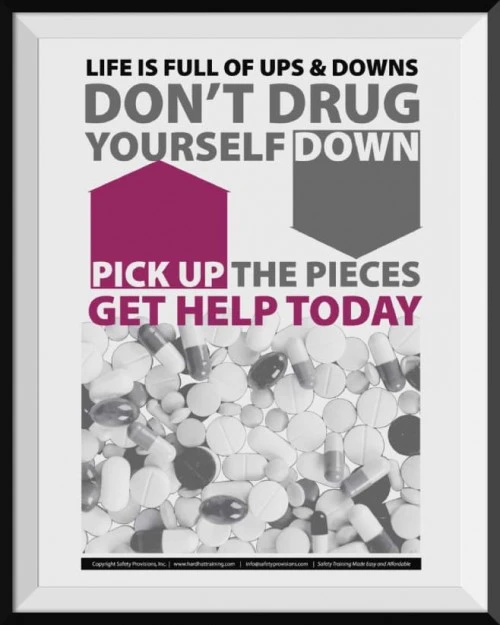
Crane operations are a constant across the globe. No matter where you go, no matter what industry you work in (construction, maritime, general industry, etc.), and no matter the time of year, it is common to see all types of cranes in action: boom trucks, knuckle booms, crawler cranes, rough terrain cranes, all-terrain cranes, overhead cranes, pedestal mounted cranes, jib cranes, the list goes on and on. It is because of their prevalence and the dangers surrounding crane operations that OSHA and the NCCCO have proposed changes to crane operator certification rules (these, of course, are not yet in effect federally, although some states, like Washington and New York, among others, have already adopted them).
And yet, as varied as crane operations and even the cranes themselves are, there are several common issues we continually encounter as we go out in the field inspecting cranes and training crane operators. Here are a few things to look out for and address prior to crane operations:
Labels: This may seem like a simple, seemingly insignificant thing, but the fact of the matter is regulations and crane manufacturer’s require that certain warning labels be on the crane and that they are legible. Too often we see cranes with labels that are covered in grime, damaged, or completely missing. If this is true for your warning decals, they need to be replaced or cleaned. Don’t just walk by them; heed their warnings. The same goes for mobile crane hand signals and load charts. By law, these need to be posted on the crane, legible and visible to the operators and personnel working around the crane. Operator controls, too, need to be properly labeled. Just because you know what they do is not an excuse.
Anti-2-Block: Take a look at this crane. We see this all of the time. The anti-two-block needs to be installed, tested, and in working condition. It is there, of course, to keep the hook and load from being pulled into boom tip and sheaves. This could several damages the crane and rigging gear or, worse, lead to a falling load and injure someone below. The justification for not having a working A2B device or not having one at all is “the work we are doing does not require us to hoist the load close to the boom tip” or something else along those lines. Well, guess what? It doesn’t matter. It needs to be on the crane.
Dead-end termination configurations: Similarly, we often see incorrectly configured dead-end terminations. The configuration pictured here is extremely dangerous. And they were lifting loads with this! Refer to your operator’s manual or to your employer for the proper ways to configure the end rope prior to hoisting a load. And make sure you have received training specific to rigging if you will be the one configuring it.
Outriggers/Stabilizers: Lastly, outrigger and stabilizer problems are equally common. Either outriggers are not extended all the way or not extended at all, or they are extended but lowered onto soil, asphalt or some other surface that is not stable enough for the pressure to come. No matter where you are extending them, you should take the time to use stabilizer pads or outrigger pads under the feet, and these pads should be load rated for the job. Several sheets of plywood or random blocks of wood may seem strong enough, but they are not okay to use. In an instant, they can crack or tumble and lead to crane instability and tip over.
Can you think of any other crane set-up and crane operation issues common to crane operations? Above all, remember this: doing the job the right way means doing the job the safe way. Sometimes that takes more time and costs a little more money. But every life preserved is worth it.