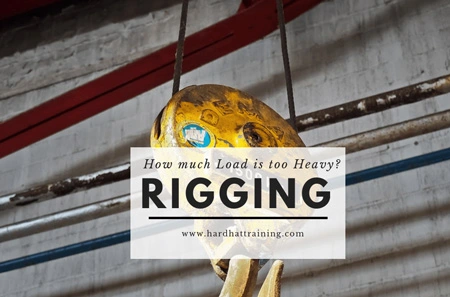
The Crane Inspection and Certification Bureau has established that crane accidents are often the direct result of negligence of the crane-related professional or the lack of adequate operator training or experience. The stark truth is that 90% of crane accidents occur due to human error.
Introduction
When rigging equipment for materials handling on a crane, you don’t want to leave anything to chance by making false assumptions. So, to stay safe and keep your job, avoid using improper rigging methods that could lead to your demise, the load’s demise, or put the crew and others in danger.
One such unfortunate case happened in Manhattan, New York when a rigging failure accident rained down debris on Madison Avenue as it fell 28 stories, leaving eight pedestrians injured with two construction workers hospitalized. Exercising the appropriate safety control measures can prevent unforeseen tragedies like this one.
Following are seven major factors that can augment the safety of hoisting and rigging equipment:
Crane Work Load Limit
Determine the weight of the load by reviewing the manufacturer’s specifications, catalog and shipping documents. Select needed equipment according to the weight and size, including the crane boom, slings, wire ropes, beams, and load. You should account for the ideal work load weight. You can calculate this number using the standard weight and apply appropriate formulas using volume and area. In general, rigging applications will require you to calculate the involved resistant forces.
Weather Condition
Consider the environment and projected forecast when planning to perform lifting or hoisting operations. Take elements such as wind direction, poor visibility, and aerial traffic into consideration. In extreme cold temperatures, refrain from performing sudden movements to rigging equipment or shock loading which can damage the brittle parts. A majority of cranes have specifications regarding the maximum wind speed that they can tolerate. There will be times when the load charts will not have specifications provided, so it is important that the crane manufacturer be consulted to establish the maximum permissible wind speed for operation.
Proper Rigging Procedure
A crucial aspect of rigging any equipment is determining the center of gravity of the load as well as the crane in order to prevent load swing. Proper sling methods should be implemented so that efficiency of the lift is increased while reducing the amount of force required. It is important to remove and secure all unused slings before lifting the load. Avoid dragging slings from under the load while ensuring that the sling angles are properly maintained. This will reduce the risks of load imbalance and falling cargo. Failure to maintain the load capacity is one of the main reasons of rigging failure.
Proper Rigging Equipment
The first step to ensuring safety for your rigging operation is choosing the right equipment. Have personnel that are familiar with the purpose of the equipment as well as its load weight tolerance. It is also important for personnel to understand the characteristics of various rigging equipment and their nature. An experienced rigger will garner the best knowledge regarding the selection of appropriate equipment for different lifts. Some of the main factors to consider are diameter, strength, grade, and the type of construction.
Inspection and Maintenance
Regularly inspect all heavy machinery and rigging hardware. Again, we go back to the idea that understanding the nature of the material and its properties will help you to determine its tensile strength. Follow inspection and maintenance for the specific equipment used. There are generally three types of inspections that every rigging hardware should undergo:
1. Visual Inspection
2. OSHA Inspection
3. Periodic Inspection
Hoist and Rigging Operator
A responsible rigging operator is essential in every industry. He should be proficient in his knowledge to oversee rigging operations safely. Requisite training and qualifications should translate to the appropriate handling of specific machinery such as cranes and forklifts. Being an operator also means that he should supervise the workforce that is under his stewardship. An operator who leaves a load suspended and unattended is liable to strict action, which may involve the cancellation of his license to operate machinery.
Signal Man
A qualified person can give crane signals to the operator. However, this person must be trained and evaluated through a written and practical test. There should only be one designated signaler at a time. If signalers will be changing between workers, the one in charge should wear a clearly visible badge of authority. This could be a colored hard hat, highly visible gloves, or a unique vest.
Responsibilities of the signaler includes:
- Be in clear view of the crane operator
- Have a clear view of the load and the equipment
- Keep persons outside the crane’s operating area
- Never direct a load over a person
Correctly attaching a load to a crane can make the difference between a successful lift and a disastrous accident. Large and heavy loads suspended in the air can lead to deadly rigging-related accidents. A small error or a brief moment of inattention and tragedy could strike. Keeping these seven rigging guidelines will ensure safety during a rigging operation, so that accidents caused by human error can be mitigated.
Safety Provisions and Hard Hat Training offers a course on rigger signalman crane safety, available at our website. For more safety training and tips, visit us at www.hardhattraining.com.