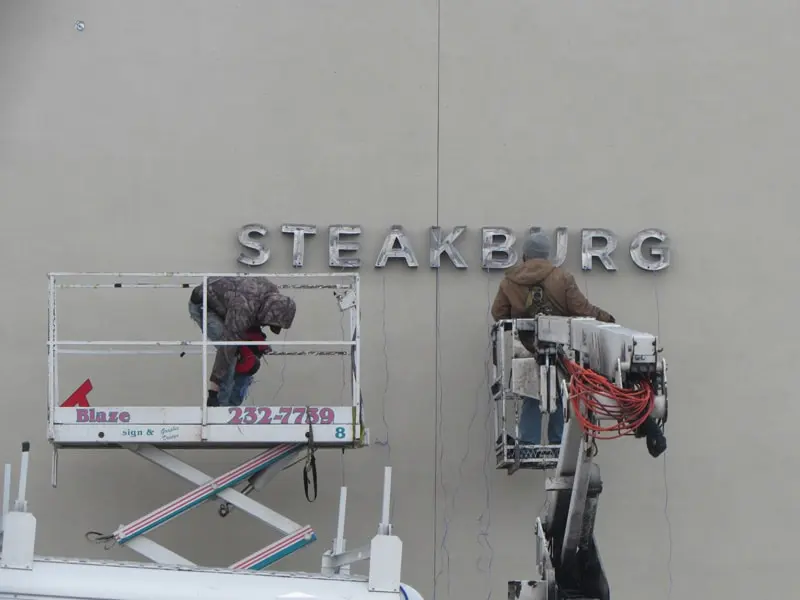
Scissor Lift Safety
When used correctly, scissor lifts are dependable and safe. However, misuse can lead to scissor lift accidents that pose significant risks to employee safety.
Misuse can be the result of an innocent mistake, but even mistakes have consequences. Knowing how to properly use and work around a scissor lift is important to your safety, as well as the safety of those around you.
When it comes to strengthening and expanding your safety knowledge, there are many resources and safety tips that are available to you. Before we dive into these, you must first understand what a scissor lift is, what it does, and what standards you must follow.
What Is a Scissor Lift?
This specific device has a controversial definition and, depending on who you ask, will vary drastically. For this section, we have created a neutral description of what a scissor lift is.
A scissor lift is a mobile platform designed to move personnel and equipment upwards in a vertical motion. Individuals can use a scissor lift for any task that would typically call for a ladder or scaffolding. Scissor lifts allow operators to carry out these tasks safely and more efficiently than they would with a traditional ladder.
OSHA Scissor Lift Safety Standards: Scaffolding
According to the Occupational Safety and Health Administration (OSHA), a scissor lift is a mobile scaffold with a vertically moving platform. OSHA does not have any standards that specifically address scissor lifts since they meet the scaffolding definition. Therefore, scissor lift operations fall under scaffolding standards and regulations.
ANSI Scissor Lift Safety Standards: Aerial Lifts
According to the American National Standards Institute (ANSI), however, scissor lifts fall under the definition of a mobile elevated work platform, or MEWP. ANSI defines a MEWP as a “Machine/device intended for moving persons, tools and material to working positions, consisting of at least a work platform with controls, an extending structure and a chassis.”
Due to this, scissor lift safety standards according to ANSI would be found under the MEWP standards and regulations.
Which Standards Do I Follow?
One of the biggest differences between OSHA and ANSI is that ANSI is voluntary while OSHA is a legal government entity and is capable of criminal prosecution. This does not mean that ANSI standards are less reliable or important. More often than not, their standards provide more details and are more specific than OSHA’s legal standards, and for this reason, OSHA may choose to enforce ANSI standards, essentially making ANSI standards mandatory to follow.
When it comes to scissor lift standards, however, regardless of how it is classified, many of the safety standards are similar since the top priority for both OSHA and ANSI is employee safety. Your workplace will determine how to classify a scissor lift and implement the associated safety standards. It is your responsibility to understand which is used in your workplace and adhere to those standards.
Scissor Lift Safety Tips
Tip #1 – Wear Your PPE
The most common PPE you should use include hard hats, gloves, hearing and eye protection, visibility vests, and slip-resistant footwear. Your employer may recommend additional PPE such as steel-toed boots or coveralls.
Scissor Lift Fall Protection
One of the most common accidents associated with scissor lift operations is falling from heights. While scissor lifts may not seem that dangerous, they can reach heights of up to 50 feet. Any fall from that height would likely result in a fatality. Therefore, it is important for employees to always wear the proper fall protection.
Fall prevention is a major concern at virtually every worksite. Yet, there is a lot of confusion about when fall protection is necessary. Some standards or locations require protection at 4 feet from ground level, while others require it at 6 feet or even 10 feet above ground level. Be familiar with and follow your industry, company, and area guidelines concerning the use of fall protection equipment.
Safety Harness
Harnesses are designed to distribute the impact of a fall. To inspect your harness, hold it from the top, then untangle and straighten any straps. Grasping the belt with both hands, bend the straps in an inverted “U” and begin looking over the harness, checking all straps and hardware on both sides for signs of damage or wear.
Lanyards
Lanyards are used to restrain and arrest falls. Like harnesses, they come in various types to be used for different applications. Familiarize yourself with your lanyard and its capabilities and limitations and take all additional training required for the safe use and inspection of the specific lanyard you will use.
Tip #2 – Avoid Unsafe Working Habits
Many operators have operated lifts for several years. While experience has made them efficient, accomplished, and well-practiced, it can however lead to bad habits. Just because you have done something a certain way for a long time doesn’t mean that it is the correct way or the safe way. If you continue to operate unsafely out of habit, it is just a matter of time before an accident of some kind will occur.
Tip #3 – Never Skip Routine Inspections
Standards require scissor lifts to be inspected both visually and functionally at the beginning of each day or shift that it is in use. Pre-shift inspections don’t have to be lengthy. They are designed to discover any apparent defects with the machine before it is put into service. These inspections help determine if the machine needs maintenance.
Tip #4 – Know Your Machine’s Limits
Balancing Point
The stability of any machine is based on the principle of balance and leverage. Understanding these principles is not difficult once you grasp a few basic concepts. The balancing point, for example, has to do with side-to-side weight distribution.
On Slopes
Know the maximum slope and grade for which the lift is rated, and never exceed it. Never depend upon the tilt alarm as a level indicator. Also, be cautious when loading and unloading from a trailer.
Extending Platform Stability
Scissor lifts with extending platforms require additional considerations when it comes to stability. When the deck extends, the center of balance shifts with it, which will affect factors such as the maximum weight and occupancy limits. To prevent tipovers while using an extending platform, strictly observe weight and occupancy limitations and follow the operating instructions when extending or retracting platforms.
Overloading
Just because you are under the required weight limit does not mean you are safe or even in line with load limit requirements. You need to account for external forces — like wind — that can introduce additional pressure on a lift, thus tipping the scale past the prescribed weight limits. Keep in mind these limits assume an equal distribution of weight.
Tip #5 – Always Consider Weather Hazards
Weather hazards are somewhat self-explanatory. You are simply looking at the current and potential weather patterns expected throughout the day and considering how they will affect site conditions, such as stability, walking-working surfaces, and visibility. Factors such as wind, rain, snow, ice, mud, and lightning are all things to be aware of and plan for. Because weather can change from what is predicted, weather risk assessments should be on-going.
Tip #6 – Working Around Power Lines
No part of the lift should come within 10 feet of a power line that is between 300 and 50,000 volts. The area within a radius of 10 feet in any direction from these power lines is an unsafe work area and must be clearly marked off on the ground by marker tape, fences, or barriers. If any part of the scissor lift could reach a power line, even if you are not working on that side, then you should use a spotter to make sure that you do not venture into that zone. If you need to get closer to the lines then they should be deenergized.
Tip #7 – Practice Safe Work Procedures
Identifying safe work procedures refers to the methods that will be used to safely complete the tasks required for the project. Applying the principles of safe work practices and procedures can seamlessly occur through identifying hazards and implementing control measures. This can also lead to the discovery of other potential hazards. Either way, as part of this section, it is important to note who will be doing what, with what tools, with what materials, at what heights, for how long, with whom, and with what safety precautions.
Tip #8 – Communication Is Key
Communication is crucial to preventing accidents and keeping everyone safe. Audible communication – either by way of radio or face-to-face – is the best form of communication. If an extended conversation needs to take place, lower the platform, engage the parking brake, turn off the machine, and take your hands off the controls before continuing.
Depending on the application, attachments, or environment, it may be necessary to use hand signals to assist with the job. You can decide what sign signifies what action, but everyone must be familiar with them and use the same signs.
Each site should have only one designated signaler. However, everyone on site should be familiar with the accepted hand signals, especially the signal for an emergency stop. This signal can be given by any person onsite at any time.
Tip #9 – Parking & Storage
When the time comes to park the lift, do so in an appropriate location. Never park in an area that would block fire lanes, emergency equipment, stairways, entrances, or exits. Park on level ground when possible. If you must park on an incline, park at a right angle to the slope, set the parking brake, lower the platform, and block the wheels. When parking on a road, use cones with a sufficient buffer to warn traffic.
Tip #10 – Standard-aligned Scissor Lift Training
Above all else, you must receive training specific to the machine type and job type. Remember, the controls and handling can widely differ from brand to brand, so in some cases, you may need additional training specific to those differences. Safety starts with proper training, and everyone — from the employer to the field supervisor to the operator — shares in that responsibility.
Luckily for you, here at Hard Hat Training, we offer a Scissor Lift Safety Training course that complies with the proper safety standards.
Hands-On Safety Training
Operators should have sufficient practice time to be proficient, safe, and confident when applying in the field what they learned in the classroom. In fact, in addition to classroom training and a written exam, regulations require lift workers to be observed operating the machine before they can be certified as a qualified operator.