Get Safety Training Today, Here Are Our Training Options
With our four different training options you have the flexibility to train when, where, and in the way you prefer.
Online Training Courses
Our fully OSHA Aligned training online is for those who prefer self-paced training from any location, or for employers who need to assign and monitor employee training progress and exam scores. Online training is a fast, effective, and complication-free method of offering construction safety training, to get your employees on their feet as soon as possible.
Our online courses allow employers to avoid hiring expensive trainers. Our curriculum provides a professional, interactive training experience while still keeping costs low.
Featured Construction Safety Training Courses
Get Safety Training Taken Care Of Now With Online Courses

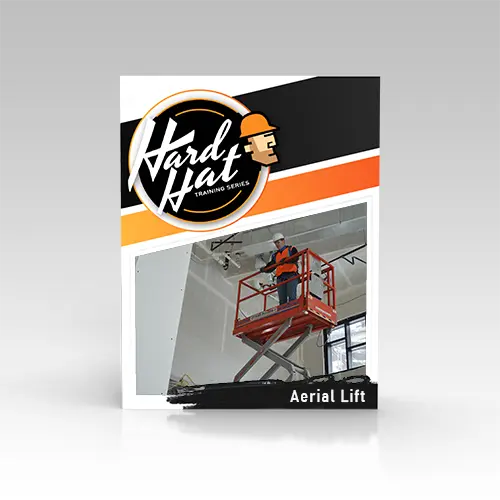
AERIAL LIFT (MEWP) – BOOM & SCISSOR CONSTRUCTION SAFETY TRAINING
Online course with OSHA Aligned training standards
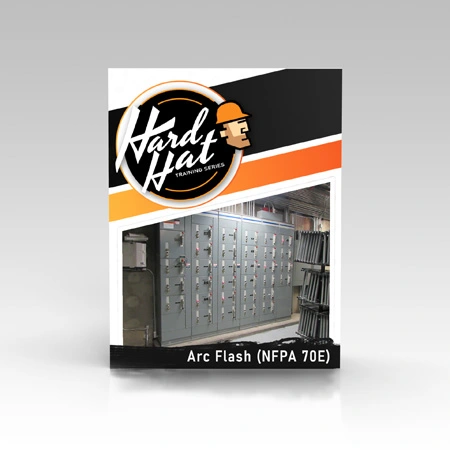
NFPA 70E (ARC FLASH) CONSTRUCTION SAFETY TRAINING
Online course with OSHA Aligned training standards
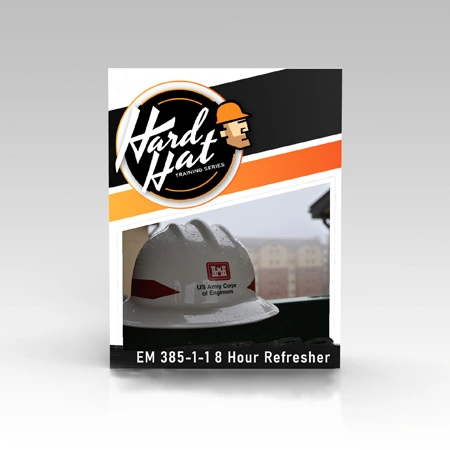
EM 385-1-1 8-HOUR (USACE) CONSTRUCTION SAFETY TRAINING
Online course with OSHA Aligned training standards
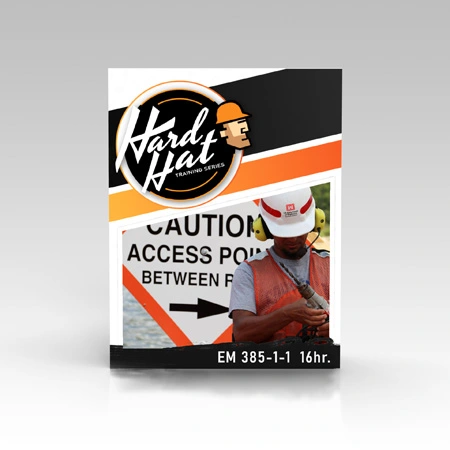
EM 385-1-1 16-HOUR (USACE) CONSTRUCTION SAFETY TRANIING
Online course with OSHA Aligned training standards
Featured Construction Safety Training Courses
Get Safety Training Taken Care Of Now With Online Courses

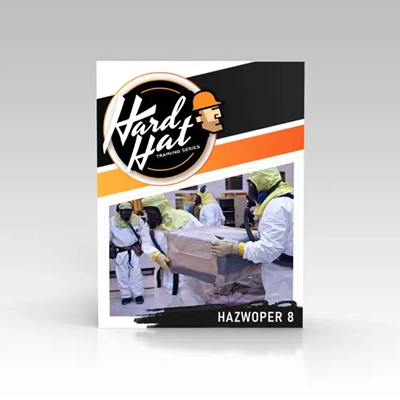
HAZWOPER 8-HOUR CONSTRUCTION SAFETY TRAINING
Online course with OSHA Aligned training standards
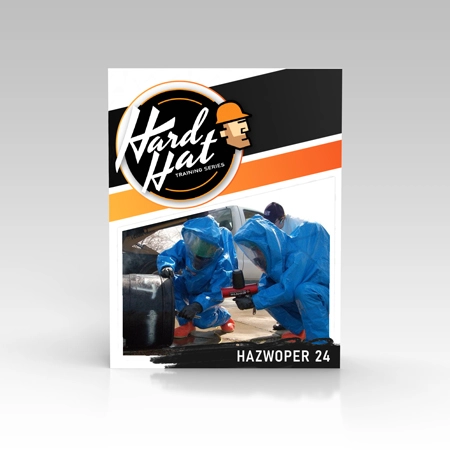
HAZWOPER 24-HOUR CONSTRUCTION SAFETY TRAINING
Online course with OSHA Aligned training standards
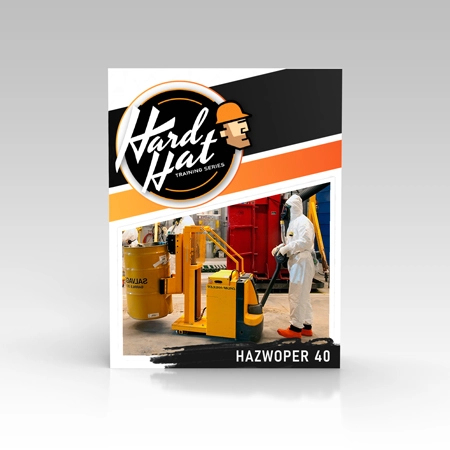
HAZWOPER 40-HOUR CONSTRUCTION SAFETY TRAINING
Online course with OSHA Aligned training standards
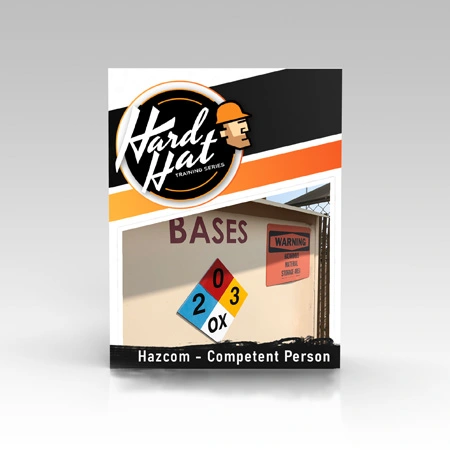
HAZCOM CONSTRUCTION SAFETY TRAINING
Online course with OSHA Aligned training standards
Recent Safety Topics We’ve Addressed
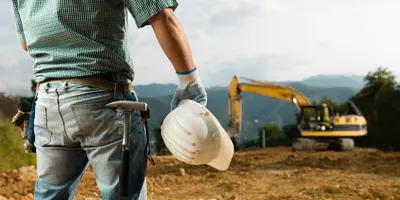
Do OSHA’s Regulations Work?
Yes, they do. Since the creation of OSHA, there has been a drastic improvement in workplace fatalities. When OSHA was founded, there were on average 38 employee deaths each day. Nowadays, the average number of employee deaths is 14 a day.
Learn the Types of Violations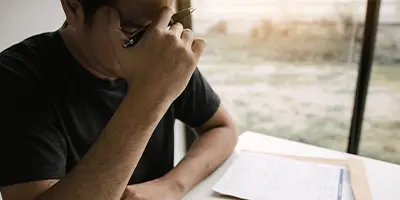
Mental Health In The Workplace
The work environment can make a huge impact on the mentality of employees. If you struggle with mental illness at work or you work alongside someone who does, it is important to communicate with your peers and keep a positive work environment.
Learn Ways to Improve Your Mental Health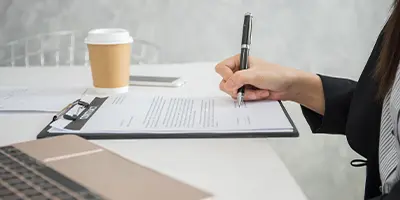
What Needs To Be Reported?
According to OSHA, an injury only needs to be recorded if it meets some specific requirements. If an injury occurs that is severe enough and it is specifically related to the work duties the employee was completing, it needs to be recorded.
Learn Specific OSHA RequirementsPurchase our OSHA Aligned online safety training courses. Become OSHA Aligned and start training today!
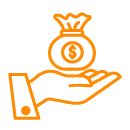
Affordable Cost
You might be wondering, “how much is it going to cost to get my entire company OSHA Aligned?” Our safety courses base prices are $39 or $79 depending which course you choose.
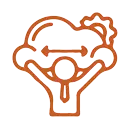
Flexible Courses
Our team is willing to work with you. We constantly update our catalog to offer additional courses that our customers need. Don’t see what you’re looking for? Request it, and we will build it for you.
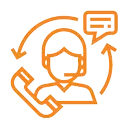
Customer Service
Our support team is ready to answer your questions. We offer three options for you to contact us: email, phone, and live chat. During hours of operation Monday through Friday, 8 AM (CST) to 8 PM (CST)
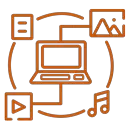
Training Options
We offer three different training solutions: DIY classroom kits, and online courses. These options allow you to select whichever format will suit your needs best.
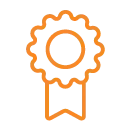
OSHA Aligned Certificate
Upon successful completion of an online course, you will be able to print off your certificate. If you bought the kit, you will then have access to and be able to issue certificates and wallet cards to those who passed.
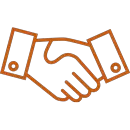
OSHA Aligned
Our writing team researches current OSHA Requirements and any pending changes. Each training is updated to meet current industry standards and regulations. We are essentially a one-stop construction safety solution.
Why Choose Hard Hat Training?
Safety Training is Important
If you were to think of your job right now, and think of all the hazards associated with it, would you think that safety training is important? If you answered yes, you’re correct. If you answered no, think again. While some jobs may not require training other jobs, have necessary safety requirements. When these requirements are not followed, or training is not given or taken seriously, it can affect everyone’s safety.
LATEST SAFETY TRAINING NEWSAvoid Violations & Fines
On any given day, it’s possible for OSHA violations to occur and not even know it. Some companies have received fines for serious and repeat violations. This article discusses four companies which are either based in northwest Ohio or with operations there that were fined a combined $135,000 for workplace safety violations. Read the article below to learn how you can avoid similar situations in your workplace.
AVOIDING SAFETY VIOLATIONSTestimonials
Learn What Makes Our Safety Trainings So Great!


“One of the best online sources for safety certifications. Very convenient and quick.”

“A really enlightening experience! Will most definitely be taking more courses from Hard Hat Training”

“Great course! Thoroughly gives you what’s needed to be safe and know what you’re doing. ”

“The course covers many forms of safety training covering most industries.”